
Making Cabochons with Handmade Tools
By Admin - October 9, 2023
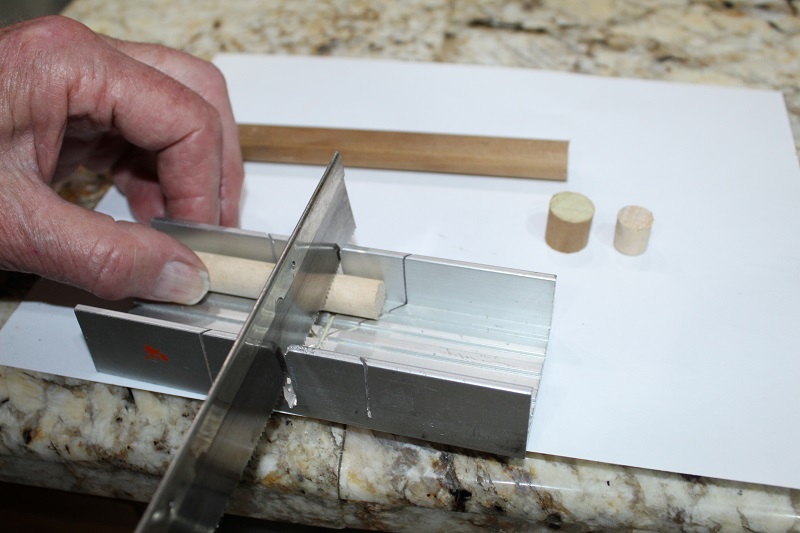
Making cabochons can seem like a daunting task to a beginner. Here are some of our tips and tricks for making your own homemade cabochon-making tools.
"For the last two weeks, I have been teaching advanced lapidary bench classes with the California Federation of Mineralogical Societies at their beautiful, forested site called Camp Paradise in the Sierra Nevada mountains. Multiple subjects are taught there including faceting, lapidary, advanced lapidary, soft stone carving, silversmithing, lost wax casting enameling and fused glass.
As a part of my classes, I teach making the tools used in carving the back and fronts of cabs. To my knowledge, these techniques are not commonly taught elsewhere.
Materials Needed
There are four different materials that I use to make my tools:
Wood dowels or wood wheels
Cratex rubberized wheels (with silicon carbide embedded into the rubber wheels)
Silicon carbide Mizzy wheels
Silicon carbide sanding blocks
Wood Dowels
The wood dowels that I use are one-half-inch in diameter. If I have a small hole to work on I use a three-eighth-inch diameter dowel. I cut them into one-half-inch length pieces and drill a small hole into the end to accept the screw end of a half-inch threaded point mandrel. I then shape them by spinning the dowel in a flex shaft unit and applying a coarse wood rasp. I use these rounded shapes to sand and polish the decorative holes that I carve into the back of cabs. To sand the sides of a groove I shape the inside of a wood wheel and use tumbling grit for the sanding media.
Shaped Wheels
The second tool that I use is made from Cratex rubberized wheels. I shape them on a diamond T-bar stone wheel dresser by holding it at an angle to the back side of the spinning Cratex wheel. I use this wheel to sand the sides of a groove.
The third tool that I make is a shaped silicon carbide Heatless Mizzy wheel. It is shaped in the same manner as the Cratex wheel. This wheel is used to carve a groove in a cab.
Silicon Carbide Sanding Blocks
The fourth tools I use in my cab-making process are silicon carbide sanding blocks. They are made from silicon carbide material and are about three-eighth-inches square and four inches long. They come in various grits from about 220-grit through 600-grit. They also come in soft binder and hard binder which is determined by how the grit is bound together. I only use the hard binder. They are used to smooth out the lumps and low places in a carving after the grinding steps. I use them to round out the top shoulder and the V of a V-shaped groove.
I cut up silicon carbide grinding wheels on my slab saw to make silicon carbide sanding blocks. When I have finished carving the top of rounded grooves on a carving, I shape the end of a silicon carbide carving block with a cylinder diamond bur to sand the top of the rounded grooves.
I find that by making my own specialized tools I can make the work on my carvings go quicker and with a better overall outcome.
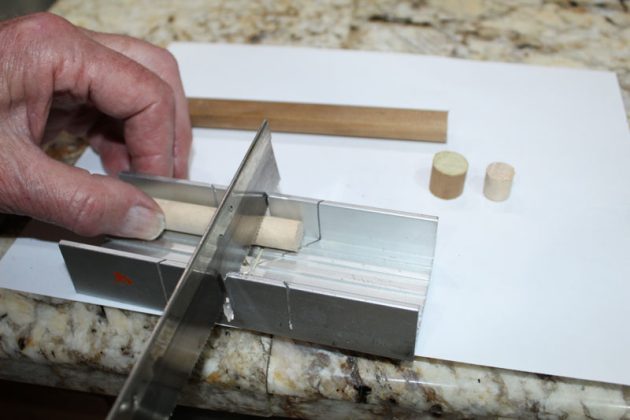
1. Xacto makes a device to help with cutting the dowel pieces.
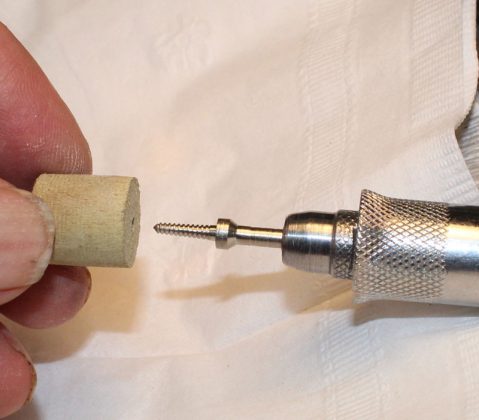
2. The dowel pieces have to be drilled in the exact center because they are installed on rotating screw mandrels.
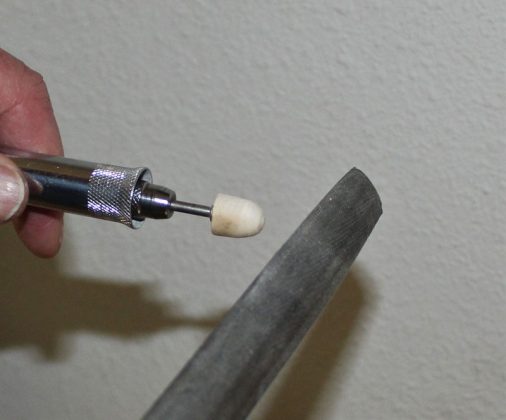
3. Shape the dowel with a coarse file.
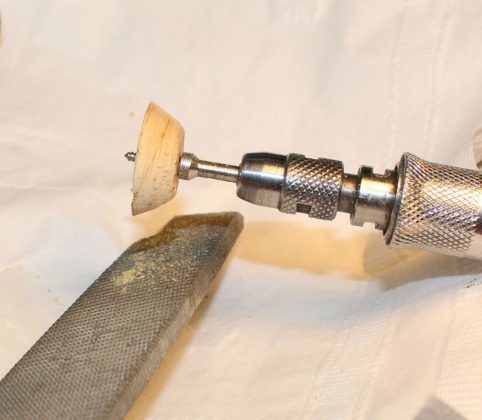
4. To sand the sides of a groove I shape a small wood wheel with a coarse file so that it has an inward slant on the inside.

5. I use a specially shaped Cratex rubberized wheel to do the coarse sanding on the sides of the grooves.
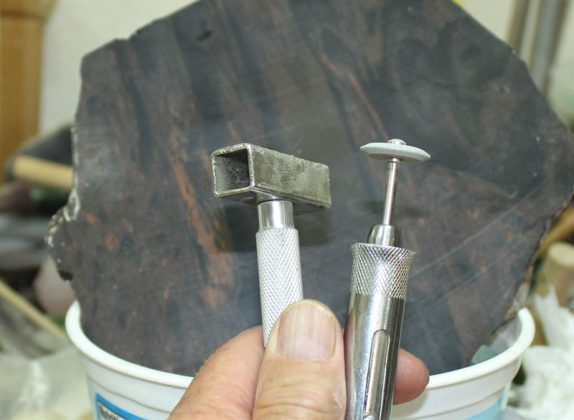
6. The silicon carbide Heatless Mizzy wheel is shaped with the diamond T bar stone wheel dresser the same as the Cratex wheel.
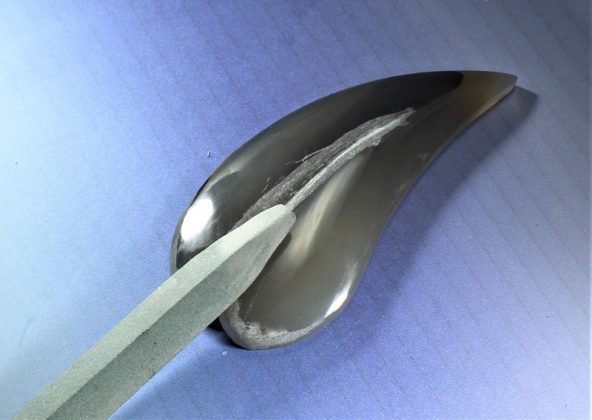
7. I started the sanding with the 220 grit sanding block.
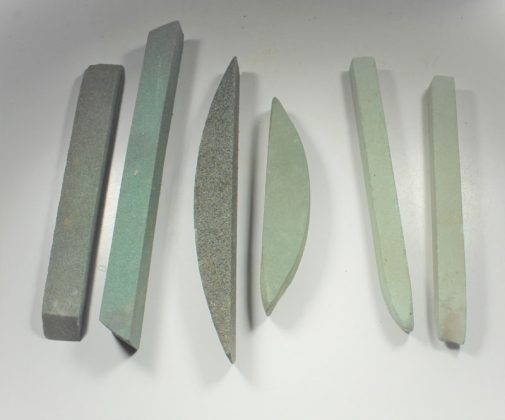
8. I cut up silicon carbide grinding wheels on my slab saw to make the silicon carbide blocks as shown on the left.
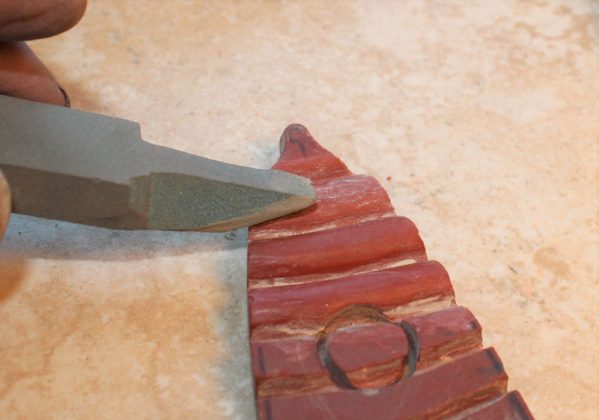
9. After I got the desired shape on the ridges I used some silicon carbide sanding blocks to sand them smooth enough for the polishing steps.
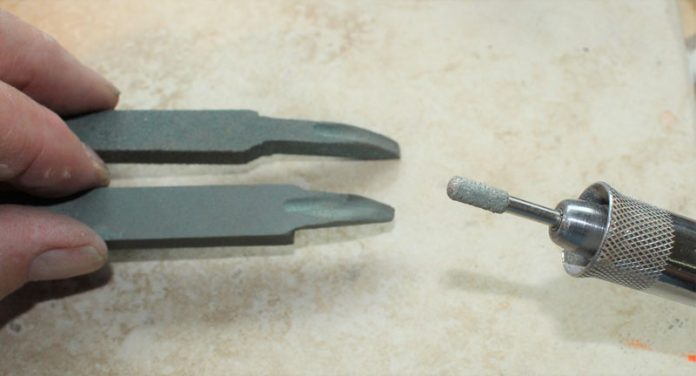
10. To shape the sanding blocks I used a cylindrical diamond bur to carve a groove into the block that would match the ridges on the carving piece. "
https://www.rockngem.com/making-cabocho ... ct+12_2023